FAQ

have questions ?
Here is a list of commonly asked questions and a variety of resources for you.
The National Fire Protection Association publishes NFPA 25 Inspection, Testing and Maintenance of Water-Based Fire Protection Systems. This document recommends that control valves without electronic supervision be checked on a weekly basis, just to make sure that they are in the open position. Other system components have different requirements. You may call Falcon Fire Sprinkler or check with the NFPA 25 or the manufacturers’ literature for details.
At least once each year, a full sprinkler system inspection should be performed by a knowledgeable professional. Some states and cities require more frequent inspections. Falcon Fire Protection, Inc. offers economical long-term service agreements. We will provide you with the test certificates which will comply with your insurance company and local fire department inspection requirements.
Buildings which are completely sprinklered enjoy special reduced rates. However, if the insurance company does not receive verification of system inspection, penalties in the form of higher insurance rates apply.
The Insurance Services Office (ISO) publishes a Commercial Fire Rating Schedule (CFRS). Section 402 of the CFRS requires building owners to have annual inspections of sprinklered systems to enjoy the “sprinklered” insurance rate.
If an inspection is overdue for up to 12 months, a 5% penalty applies. If the inspection is overdue for 12-24 months a 20% penalty applies. If an inspection is 24-36 months overdue, a 60% penalty applies. If after 36 months an inspection is still not performed, a fully sprinklered building is rated as “Unsprinklered” for the purpose of insurance, with no credit allowed.
Check with your insurance carrier about the rate for your building. Even though it is fully sprinklered you may not be getting as big a discount you’re entitled to. Get your sprinkler system inspected and take full financial advantage of your fire sprinkler system.
This document is provided for information purposes only. It is not intended to be a substitute for individual legal counsel or advice on issues discussed within. Readers seeking resolution of specific legal issues or business concerns related to the captioned topic should consult their attorney and/or insurance representative.
Introduction
A fire pump is an integral component of a total fire protection system. A fire protection system at a facility may include automatic sprinkler systems, standpipes, hose stations, and/or fire hydrants. The purpose of a fire pump is to provide or enhance the water supply pressure from public mains, suction tanks, gravity/elevated tanks, lakes, and other bodies of water.
Listed and Approved
The pump, driver, controller, and auxiliary equipment should be U.L. Listed (Underwriters Laboratories) and/or F.M. Approved (Factory Mutual) to ensure that the equipment has been thoroughly examined and appropriately tested for fire pump installations.
NFPA 20, Standard for the Installation of Centrifugal Fire Pumps requires the use of listed equipment, or approved equipment, or both. Under the testing and listing approval system, the manufacturer is responsible for providing a listed or approved pump that will perform satisfactorily when installed in conformance with NFPA 20. Individuals responsible for installing the pump and auxiliary equipment must also follow the provisions of NFPA 20.
Types and Characteristics
The two most common types of fire pumps are the horizontal-shaft centrifugal pump and the vertical-shaft turbine pump. The horizontal shaft centrifugal pump is one in which the pressure is developed by impelling water outward from a center of rotation. The impeller is mounted on a horizontal shaft. The vertical shaft centrifugal pump is similar, but the impeller is mounted on a vertical shaft.
These pumps can be driven by electric motor, internal combustion engines, or steam turbine. Fire pumps are available with rated capacities from 25 to 5,000 gallons per minute (gpm). Pressure ratings range from 40 to 394 pounds per square inch (psi) for horizontal pumps and 26 to 510 psi for vertical-shaft turbine pumps. Note that natural gas, L-P Gas, or gasoline engines are not recognized by NFPA 20.
Horizontal-shaft centrifugal fire pumps are required to be installed to operate under positive suction head (e.g., municipal water supply). For new installations, NFPA 20 no longer allows the use of horizontal centrifugal fire pumps taking suction under lift (e.g., from a pond, reservoir, lake, etc.). If the water supply is such that suction lift cannot be avoided, a vertical-shaft turbine fire pump should be installed.
Fire pump design characteristics provide maximum reliability and specific head-discharge in psi (pounds per square inch). Fire pumps are designed to provide their rated capacity with a built-in safety factor (150 percent of rated capacity at 65 percent of rated pressure) to provide a cushion in the event that there is a greater than expected demand at the time of a fire.
Auxiliary Equipment
Fire pump accessories have an important bearing on the complete functioning of a fire pump. An understanding of the following auxiliary equipment is worthy of attention.
A motor controller is a critical component to ensure the successful operation of the pump. The controller includes timers, disconnecting means, circuit breakers, and similar devices.
The power supply to the fire pump should be positioned upstream from the facility’s main electrical disconnect. In the event of a fire, this will allow the fire pump to continue to run, even though the power to the facility has been disconnected (e.g., standard operating procedures for the fire department may be to disconnect the main power supply to minimize the danger of electrical shock to fire department personnel). All electrical wiring should be in accordance with NFPA 70, National Electrical Code.
Circulation relief valves are used to prevent the pump from overheating. Their function is to open at slightly above-rated pressure when there is little or no discharge, so that sufficient water is discharged. These valves are not needed on diesel pumps where cooling water is taken from the pump discharge.
Relief valves are required on the discharge line when the operation of the pump can result in excess pressure.
Jockey pumps maintain pressure in the underground, compensate for leakage, and reduce the number of times the fire pump starts. Jockey pumps are not needed on all fire pump installations; however, they are usually found were there is an extensive underground piping system. They are equipped with gauges, control valves, and a check valve.
Hose valves are used in testing pumps. 2 1/2” valves are attached to a manifold placed outside the pump room to avoid any damage to the pump, driver, and controller.
Pump Room
Pump rooms and power facilities should be as free as possible from exposure to fire, explosion, flood, and windstorm damage. Light, heat, ventilation, and floor drainage should be provided for pump rooms. Pumps should be located in fire resistive or non-combustible buildings. A dry location above grade is recommended. Pump rooms should be large enough to accommodate personnel as well as all equipment and devices for inspection, maintenance, and testing.
Flushing and Hydrostatic Tests
New fire pump installations require the suction piping to be flushed at designated flow rates or at the hydraulically calculated demand rate of the system, whichever is greater. The designated flow rates are dependent upon the size of the suction pipe. (Refer to the following table.)
Pipe Size (Inches) | 4 | 5 | 6 | 8 | 10 | 12 |
Flow (GPM) | 390 | 620 | 880 | 1560 | 2440 | 3520 |
Suction and discharge piping should be hydrostatically tested at not less than 200 psi pressure, or at 50 psi in excess of the maximum pressure to be maintained in the system, whichever is greater. The pressure should be maintained for two hours.
Field Acceptance Tests
Field acceptance tests are required when a new fire pump has been installed. This test procedure ensures that the pump, driver, controller, and auxiliary equipment has been properly installed and is operating per the manufacturer’s specifications. The pump manufacturer or a representative should be present during the field acceptance test.
Inspection, Maintenance, and Testing
The building owner or a representative (e.g., management company) is responsible for the maintenance of the fire pump. Fire pumps should be inspected, maintained, and tested per the manufacturer’s specifications. If the manufacturer’s specifications are unavailable, refer to the standard for the maintenance of fire pumps NFPA 25 (Standard for the Inspection, Testing, and Maintenance of Water-Based Fire Protection Systems) or The Hartford’s Automatic Sprinkler Systems Inspection, Maintenance, and Testing Procedures Guide.
A comprehensive maintenance program is generally broken down into three components: inspection, maintenance, and testing.
Inspection: A visual examination of the fire pump to verify that it appears to be in operating condition and is free of physical damage. Examples include:
- Heat in pump room is minimum 40 degrees F (70 degrees F for diesel engines)
- Pump suction, discharge, and bypass valves are open.
- Controller pilot light (power on) is illuminated.
Maintenance: The work that is performed on the fire pump to make repairs or to keep it operable. Examples include:
- Lubricate pump bearings
- Clean pump room louvers
- Clean strainer and filter in diesel fuel system
Testing: A procedure used to determine the status of the fire pump and auxiliary equipment by conducting periodic physical checks. Examples include:
- Conduct a weekly churn test (run pump without water flowing)
- Conduct an annual full-flow performance test
- Operate alarm, supervisory, and trouble signals
Analyze Inspection, Maintenance, and Test Results
The building owner or a representative should analyze inspection, maintenance, and test results to ensure that the fire pump and auxiliary equipment is working properly. Where the results have identified deficiencies, steps should be immediately taken to correct the problem(s). This important step is often overlooked, potentially leaving fire pumps inoperable. Be sure to include this step in the overall fire pump maintenance program.
What to Do When a Pump Doesn’t Operate Properly
Measures should be taken during an impairment to ensure that increased risks are minimized and that the duration of the impairment is limited. NFPA 20 provides a trouble-shooting checklist to help in identifying causes of pump problems. Qualified personnel must make the necessary repairs and adjustments to ensure proper pump operation.
If the pump output is so deficient that it will not properly supply the required water pressure for the total fire protection system, an appropriate Impairment Program (e.g., notify the fire department, institute a fire watch, discontinue hazardous operations, etc.) should be incorporated, and repairs should be completed as quickly as possible.
Conclusion
Understanding the proper selection, installation, and maintenance of a fire pump can make the difference between business as usual and a catastrophe at a facility.
Ensure that:
- (1) a pump, driver, controller, and auxiliary equipment is U.L. Listed or F.M. Approved
- (2) the appropriate type of pump and auxiliary equipment is selected and properly installed
- (3) the pump room and power facility is free from fire, explosion, flood, and windstorm damage
- (4) for new installations, flushing, hydrostatic and field acceptance tests have been conducted
- (5) a comprehensive inspection, maintenance, and testing schedule has been incorporated in the facilities overall preventive maintenance program.
References
- AISG Fire Protection Bulletin, “Fire Pump Maintenance,” Number 43.04
- The Hartford, Automatic Sprinkler Systems, Inspection, Maintenance, and Testing Procedures Guide
- NFPA 20, Standard for the Installation of Centrifugal Fire Pumps
- NFPA 25 Standard for the Inspection, Testing, and Maintenance of Water-Based Fire Protection Systems
- NFPA Fire Protection Handbook, 18th Edition, Section 6, Chapter 4.
This document is provided for information purposes only. It is not intended to be a substitute for individual legal counsel or advice on issues discussed within. Readers seeking resolution of specific legal issues or business concerns related to the captioned topic should consult their attorney and/or insurance representative.
Backflow: the flow of any foreign liquids, gases, or substances into the distributing pipe lines of a potable supply of water. Backflow may occur under two conditions–pressure greater than atmospheric, and pressure that is subatmospheric.
Back Pressure: backflow caused by a pump, elevated tank, boiler, or other means that could create pressure within the system greater than the supply pressure.
Back Siphonage: a form of backflow due to a negative or subatmospheric pressure within a water system.
Cross Connection: any connection or structural arrangement between a public or a consumer’s potable-water system and any nonpotable source or system through which backflow can occur. (Bypass arrangements, jumper connections, removable sections, swivel or change-over devices, and other temporary or permanent devices through which, or because of which, backflow can occur are considered to be cross connections.)
Double Check Assemblies: Protects the potable water supply from a pollutant caused by a cross connection. Only used in a backpressure condition. Consists of two independently operating check valves, two shut off valves, and four test cocks. Used in low hazard conditions.
Double Check Detector Check Assembly: Protects potable water systems from a pollutant caused by a cross connection on a fire system and also detects any unauthorized use of water and leaks on the fire line system. Only used on a backpressure condition. Consists of two independently operating check valves, two shut off valves, and bypass assembly with meter. Used in low hazard conditions.
Reduced Pressure Principle Backflow Prevention Assembly: Protects the potable water supply from contamination caused by a cross connection. May be used on a back siphonage and back pressure condition. Consists of two independently operating check valves, a hydraulically operated mechanical pressure differential relief valve located between the check valves and below the first check, two shut off valves, and appropriate test checks. Used in high hazard conditions.
Reduced Pressure Detector Assembly: Protects the potable water supply from contamination caused by a cross connection on a fire system and also detects any unauthorized use of water and leaks on a fire line water system. May be used on a back siphonage and backpressure condition. Consists of two independently operating check valves, a hydraulically operated mechanical pressure differential relief valve located between the check valves and below the first check, two shut off valves, bypass assembly with small diameter RP and meter, and appropriate test checks. Used in high hazard conditions.
The following matrix identifies comparable valves made by competitors to the Ames line of backflow preventers.
|
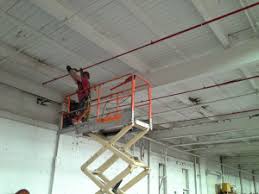